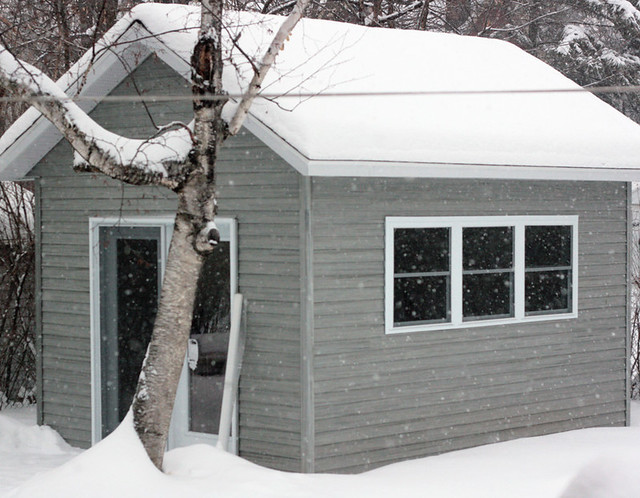
I think that it's time that I share a few shots of the inside of the studio with you all. I know you've been patiently waiting for the big reveal, and I really wanted to show you, but the truth is, it's just not that interesting! The studio is working out extremely well, it's super practical and does everything that we need it to, but it's sparse. It's not a super artistic, inspirational space just yet. It's white, stainless steel, clean and very bright. The ceilings are vaulted, the windows are large, so the space is flooded with natural light and even though it's a modestly sized studio (it's only 10' x 14') it feels wide open and spacious.
Chris does most of the production dyeing for TFA. Together we come up with the colourways, figure out the recipes and then when the orders start pouring in Chris gets to work. All of the colourways are dyed in small batches of 5-10 skeins at a time depending on the fiber content. The Silver Label Mulberry Silk and the Purple Label Cashmere Sock yarn take the dye differently then the 100% merino yarns, so they require a different application. The process is quite simple and doesn't require anything more potent then plain white vinegar and heat to set the colour. I often wonder what the cashiers at Costco think of us when we roll up to the cash with twenty 5L containers of vinegar. I'm sure that they think we're crazy enthusiastic picklers!

Since Chris is a bit of a neat freak he has stapled cardboard to the "backsplash" in order to catch some of the dye splatters. I'm completely against this and can't wait for him to realize that the cardboard is a mistake and the multicoloured dye splatters are what make the space beautiful. I'm sure that he'll come to this conclusion on his own, I'm patiently waiting.
We have two long stretches of stainless steel tables, each with it's own sink. We've divided the space up into a clean side and a dirty side, the dirty side is for dyeing and the clean side is mostly for rinsing. The stainless steel surfaces are awesome. They make the whole clean up process so much easier. Just a quick squeegee into the sink and you're ready to go with the next colourway.

It's not high-tech and it's not fancy. Chris has started decorating the walls with some pretty random artwork. Eventually I hope that the walls will be covered with art and splashes of colour. I'll share photo's again in the summer when the space is more lived in and we've had a chance to "pretty up" the exterior. Since everything has been frozen for months we haven't done anything to our plain little studio yet.
We thought long and hard before we decided to take the plunge and invest in our own studio. We knew that we needed a change, we couldn't continue to dye at the pace that we needed to in the laundry room. We have seriously considered renting a space many times, maybe even hiring a few people to help with the production, but in the end we always come back to the fact that we love being a small, family run business. We love working from home and having flexibility. If we rented a space and hired dyers we would suddenly be a much different company. We would have to worry about making enough money to pay the dyers, pay for the space. We would spend much more time "working". The way we're organized now, it rarely feels like work. Don't get me wrong, we're up every morning, Monday to Friday, and we dye and ship hundreds of skeins of yarn every week. But the work is fun and so rewarding. Staying small means that we're always able to work together and that we have the time and energy to devote to dreaming. Sounds whimsical doesn't it? But it's such an important part of staying creative. We need to be able to take an afternoon every once in a while to play with colour, to experiment, to not worry about the orders and just make.